We’ve taken pride in the quality of our craftsmanship for over a century, and in keeping with that tradition, the Filson Restoration Department and Filson Workshop were formed. We caught up with Jeremy Bennett, Jon Duce, and Marissa Barnard from the workshop team to find out what goes into restoring a Filson original and creating a one-of-a-kind piece from salvaged resources.
Why were the Filson Restoration Department and Filson Workshop formed? To which purpose have they served?
Jeremy – Filson Restoration Department and Filson Workshop were created from a desire to reduce the amount of waste Filson was contributing to the local landfills. We realized we had amassed a large inventory of products that had been decommissioned through our returns and repairs department and had simply reached the end of their product life cycle. Restoring the items just seemed like the right move and the only move.
Why are these departments important to Filson?
Jeremy – Both the Restoration Department and Filson Workshop have proven to be great sources of information from many different perspectives of our business but most influential in product design and development.

The restoration department allows probably more creative freedom in design – what do you look at for inspiration?
Jon – I like to look at the past to see what worked then. Things were built to last and be serviceable; tools, machinery even workwear, not to just be consumables that end up in the junk pile.
Marissa – One of the best things about working at Filson is that there is such a rich history and distinct point of view that has been established over the years. Design can therefore almost feel instinctual. We get to play with the classics, which are often hard to improve upon while getting to add our twist. However, much of our process is limited by the materials available to us. We have such an eclectic mix of fabric, leather, and hardware at our disposal that we have to be very intentional with how we put our pieces together. There is a huge amount of creative problem solving involved in building products around unusual or unconventional materials. These types of challenges are my favorite part of the job. Creating something new and beautiful out of something that would otherwise end up in the trash is incredibly rewarding.
Have there been any unique restoration stories – special product for a customer, family heirlooms?
Jeremy – We recently had a customer bring in his father’s old heavily worn out medium duffle bag that had gone through our repairs/returns process and was deemed unrepairable. Our retail staff connected him with the Restoration team to discuss a custom restoration on his bag which he was more than happy to pay for. During the restoration process, he also requested to have some of his grandfather’s military service patches sewn onto the bag along with some other heirloom items from his grandfather. It was truly an honor for the team to be a part of such a unique restoration.

What elements of your past have contributed to your work with Filson?
Marissa – I grew up around artists and makers, and crafting has always been a huge part of my life. My mom taught me how to sew at a young age and I spent a lot of time as a kid repurposing whatever we had around the house into experimental projects. A few years ago, I decided to make what had always just been a hobby into a job and went back to school for apparel design.
Jon – I have no specific formal training, but I’ve always had a passion to work with my hands, repair, and design. I’ve done everything from finish carpentry to welding and fabrication. It all started by using a home sewing machine for repairing/altering my jeans and small upholstery projects. From that point on I’ve loved working with and restoring garments and bags.
What challenges do you run into and how do you solve those problems?
Marissa – We have such a wide range of materials we get to work with but often very limited quantities of those things so we spend a lot of time creatively problem solving around our limitations. You have to constantly be adapting and reworking your ideas at every step to make sure you have what you need to get the job done. Because we make everything by hand and do every step of the manufacturing process ourselves, we have to know how to perform a huge range of functions, all up to Filson’s high standards. You have to be curious and resourceful to get stuff done. Sometimes the learning process is rough but mastering new skills is always exciting.
Jon – It can be difficult working with bags that have been damaged to the point where the overall shape is very distorted and stretched. You really have to manipulate the pieces when sewing them back together to retain the bag’s original shape. The best way to overcome some of these issues is to make sure to make plenty of witness marks on the bag and just take your time.
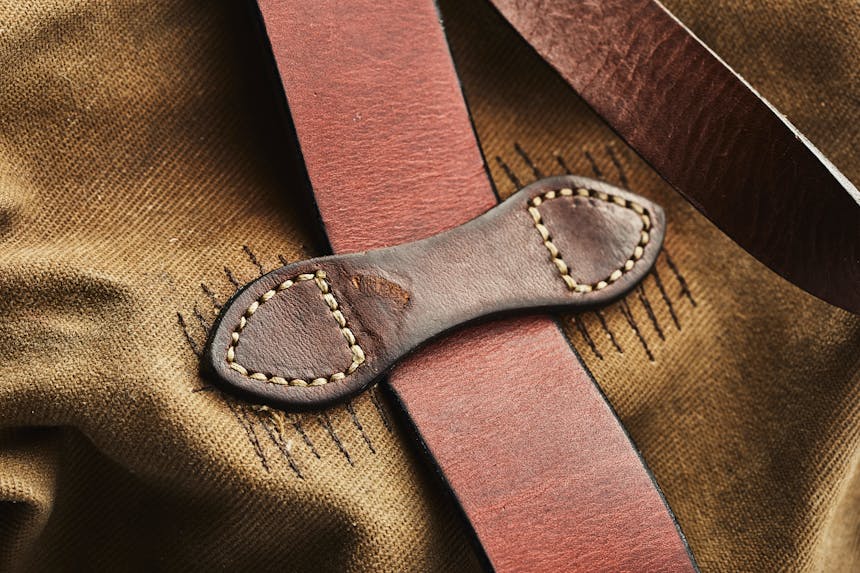
What helps distinguish Filson’s operation from other brands?
Marissa – Filson’s legacy of quality craftsmanship is hard to beat. Giving us the chance to extend the life of our products even further makes perfect sense for a place committed to making things that will last a lifetime.
We utilize a lot of Bridle Leather and Tin Cloth in our products. What is the significance of these materials?
Jeremy – Bridle leather has been around for hundreds of years and used for countless jobs, from industrial machine pulleys to horse tack, and has proven to be an incredibly durable material. Not only does the bridle leather last for years, but it also ages beautifully if properly cared for. The aniline finish (non-pigmented leather that retains the hide’s real nature) of Filson’s bridle leather allows the user to inadvertently create their own custom patina through the ways they use the product. This same patina process holds true with our oil Tin Cloth and Rugged Twill materials. Both of these fabrics have a wax finish that reduces friction wear and increases the longevity/durability of the product. The unique characteristics of our Filson materials are what make the restoration products so interesting.

What is the oldest bag you’ve restored?
Marissa – I just restored a Forestry Cloth Cruiser from the ’70s. It was really cool to see how well it had held up despite the regular use it got. Someone had clearly tried to repair it several times, which gave it lots of extra character and just goes to show how much people love their Filson stuff. It never gets old looking at how each piece gets used and the different ways a fabric or design can age depending on who was wearing it and what they were using it for.
Jon – I’ve restored a few bags that were roughly 20-23 years old. They’ve got a lot of patina and wear so they end up looking really cool. One of my favorites was a Medium Duffel Bag from the mid-’90s. It was absolutely destroyed but the leather was in pretty decent condition. Got it all stitched/patched up and was good to go!
What projects have you worked on this year with Filson Workshop that you are most excited about?
Jon – I’m pretty pumped about our line of workshop leather goods that we drew inspiration from bags and pouches that mountain men and trappers used. Because these bags aren’t mass-produced, extra care is taken during the design and construction process. Each panel, pocket, and strap is hand-cut and the wallet is even hand-stitched.